Hondaでは次世代BEV開発に向けて、エネルギー効率化を軸にした熱マネジメントの高度化や、バッテリー技術のさらなる革新に取り組んでいる。「Honda Tech Talks#11」では、実際に現場でチャレンジに臨んでいるエンジニアたちが登壇。高効率BEVシステムの開発や、EVバッテリーの効率的な生産、安全性への取り組みなどについて語られた。
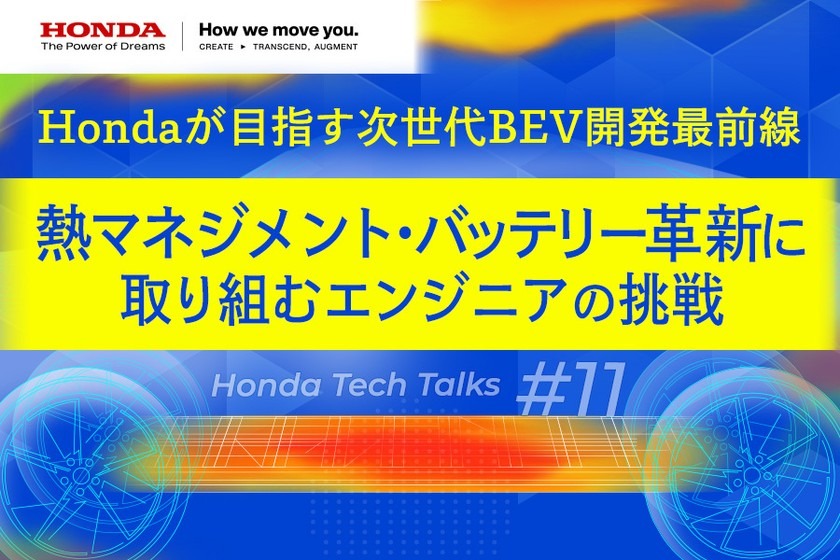
この記事に登場する人
INDEX
アーカイブ動画
カーボンニュートラル実現に向け、高効率なBEVの導入など電動化をさらに加速
エネルギーシステムデザイン開発統括部
BEVシステム開発部
部長
西 智弘
最初に登壇したのは1999年に入社以降、長年にわたりエンジン開発に携わってきた西 智弘だ。現在はBEVのパワーユニットシステム領域の開発責任者を務める。
人々が行動する「パワー、原動力」を提供するとの理念を掲げるHondaでは、時代やニーズが変わっても、クルマはもちろん船外機や航空機など、毎年約3000万台のパワーユニットを世に送り出し続けている。
Hondaでは2050年までに、全製品ならびに企業活動におけるカーボンニュートラル、交通事故死者ゼロを目標に掲げており、クルマの電動化に向けては10年ほど前から注力。これまで累計350万台以上の電動車を世界に展開してきた。
「高効率なBEVの導入など、さらに電動化を加速させていきます」と、西は今後の展望についても力強く語った。
高効率なBEVが社会に広まれば、従来のようにエネルギーを享受する側であったモビリティが、エネルギーを供給する側、つまり新たな社会インフラ・電力貯蔵媒体としての役割を担うようにもなる。
実現に向けてはバッテリーそのものの進化はもちろん、パワーユニットやパワートレーンに無駄なくエネルギーを伝える高効率なBEVシステムが重要だ。
さらには先述したような地域や社会など、クルマ以外に供給する「V2X(Vehicle to Everything)」と呼ばれるエネルギーエコシステムなどを構築していく必要がある。
現在は国内外でさまざまなBEVのラインナップが拡大している。ラスベガスで先日開催されたCES2024で公開された0シリーズは、EV専用のプラットフォームならびに新たなE&Eアーキテクチャで開発されたモデルで、2026年市場に投入される予定だ。
このように、着実に社会導入されているBEVだが、「価格が高い」「充電に時間が掛かる」「航続距離が短い」といったペインポイントがあり、熱源となるエンジンがないことから特に冬場のエネルギー消費が激しい、と西は語る。
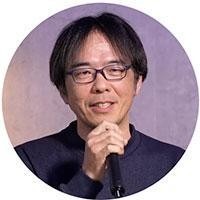
エンジン車と比べて構造がシンプルなため、これ以上電費を上げるのもなかなか難しい。そこで、我々はエネルギーマネジメントの技術を高めることに取り組んでいます。
冬場の航続距離を伸ばすために、ヒートポンプ技術などを活用し電費の向上を実現
エネルギーシステムデザイン開発統括部
BEVシステム開発部 BEV性能開発課
チーフエンジニア
安藤 聡
2006年にHondaに入社した安藤は、AWD(All Wheel Drive:全輪駆動)やHybridのパワーユニットシステムなど、長年にわたり駆動系の開発に従事。現在は0シリーズのBEVパワーユニットシステムの研究開発責任者を務めている。
安藤はまず、BEVのパワートレーンシステムを紹介した。エンジンやモーターといったパワートレーンで発生したエネルギーを、タイヤなどに効率よく伝えるための装置やシステムであり、バッテリーチャージャー、コンバーター、冷却モジュール、先述したV2Xなども含まれる。
パワートレーンシステムを構成する各パーツやシステムを、それぞれが高い性能レベルを発揮させるだけでなく、共通性を持たせることでコスト削減も両立させる開発に取り組んでいる。
高い性能を実現させるために、まずは航続距離やバッテリーの耐久性など、車両としての大きな目標を掲げる。
そして、それぞれの目標が関係するシステムに落とし込む。さらにブレークダウンしていき、コンポーネント単位まで落とし込んでいく。
数多くある目標の中から、本講演では冬季の航続距離目標を実現するためのアプローチについて解説。まずは、航続距離とはどのように決まるのかを紹介した。航続距離は電費(エンジン付き車両で言う燃費)とバッテリーの容量で決まる。電費はスライドで示されたように、モーターなどのパワーユニット(PU)系、走行時に受ける抵抗、オーディオやライトなどの12V系消費電力、エアコンの消費電力やクルマに搭載されたそれぞれのユニットの消費電力によるところが大きい。
中でも多くの電力を消費しているのが、オレンジ色の矢印で示された空調と青色の矢印で示された走行抵抗である。EV車は減速時にエネルギーを回収できるため、「ボリュームも大きい減速エネルギーを回生して、いかに取りこぼさないかも大きい」と、安藤は補足した。
スピードと電力消費の相関図も示した。車速が低いときには空調の影響が、一方、車速の上昇に反比例するように、今度は走行抵抗の影響が増えていくていくことが分かる。
このような特徴を踏まえ、充電ならびに走行時にパワートレーンから発生する熱でバッテリーを加温する。さらには空気内の熱エネルギーを集めるヒートポンプ技術も活用し、車内の暖房に活用することで、電費を上げていくことを目指した。
ヒートポンプシステムの実現には、外気の熱を回収する熱交換器が必要であり、ラジエターよりも前面、フロントグリルのすぐ後に配置した。
だが、1つ懸念があった。熱交換器への霜の付着(着霜)である。「ただこの時点では、大丈夫だろうとの思い込みで開発を進めてしまいました」と、安藤は振り返った。
しかし、懸念であった着霜問題が、次第に顕在化してきた。そこで安藤は改めて、解決に向けて動いた。
そもそも着霜すると、どのような問題が生じるのか。霜を除去するためにはどのような運転を行えばよいか、などである。
熱交換器単体でのテストも行うこととした。スライド一番左の画像が常温の状態で、霜は付着していないことが分かる。これが中央の写真、外気温2℃になるとかなりの範囲に付着している。
そして右側の写真、外気温が0℃になるとすべての面で着霜が発生し、ヒートポンプ機能は動作しなくなることが明らかになった。さらには後方のラジエターにも外気が通らないため、走行にも問題が出ることが分かった。
どうすれば着霜を防ぐことができるのか、安藤はHondaに根付く問題解決フレームワーク、ワイガヤを実施することとした。
ワイガヤとは、メンバーがワイワイガヤガヤと課題の洗い出しや解決策を議論するHonda独自のカルチャーである他の意見を否定してはならない、というルールも定められている。
ワイガヤの結果、どのような気象の条件下で着霜は起きるのか。着霜が実際に起きやすい地域はどこで、どの程度の頻度で起こるかなどを、改めて検証した。すると、アメリカのウォータータウンという地域の冬季に、41%という高い頻度で起きることが分かった。
そこで安藤らは、これまでのHondaの故障発生時の走行性能の考え方を参考に、完全に着霜したとき、90%着霜したとき、それぞれの走行目標を設定すると共に、アラートランプでドライバーに伝えるなどの施策を検討していった。
一方でHondaには、現場、現物、現実を見て物事を判断するべきとの「三現主義」という考え方がある。安藤はこちらも実行している。
日本においてウォータータウンに近い気象条件のエリアをピックアップし、現地に赴き、実車を使ってどの程度着霜するのか、その際の走行性能はどうなのかといったデータを検証した。
すると実テストではほぼ着霜は見られず、窓を全開にして走行するなどエアコンに負荷を与えても、変わらなかった。外気吸熱の使用が限定的だと予測し熱交換器の配置場所をラジエターの前に置くことで、着霜問題を解決した。
さらには、他の熱マネジメントオペレーションも最適化することで、「目標としていた冬季の航続距離を達成することができました」。安藤はこのように成果を述べ、セッションを締めた。
エネルギーエコシステムの起点となる、さまざまなバッテリー関連技術を研究開発
次のセッションは、大金 崇、松本 充功、冨沢 佑一が登壇し、0シリーズにも適用されるHonda EVの中核をなす技術、バッテリーシステムの開発について解説した。
エネルギーシステムデザイン開発統括部
エネルギーストレージシステム開発部
エネルギーストレージシステム開発課
課長
大金 崇
まずは、2000年の入社以来25年間一貫して、バッテリーシステムの開発に従事してきた大金が、現在の状況や技術領域などを紹介した。
冒頭で西が紹介したように、Hondaは2050年までに全製品、企業活動におけるカーボンニュートラルならびに、環境負荷ゼロの循環型社会の実現を目指しており、大きく3つの軸で進めている。
安藤が紹介したように、それぞれの領域で目標値を掲げ、実現に向け取り組んでいる。バッテリーの開発はエネルギーエコシステムにおける重要な起点と捉えている。
3人が所属するエネルギーストレージシステム開発部では、バッテリーそのものの技術開発からバッテリーシステム、さらには充給電システムといった領域まで担う。
今回の説明は0シリーズのコンセプトでもある、大容量でありながらThin(薄く)、Light(軽く)なバッテリーパックの開発に焦点をあてて、具体的な技術解説については他の2名に解説を委ねると述べ、大金はバトンを渡した。
小型・薄型バッテリーパックシステムの安全性向上に向けた取り組み
エネルギーシステムデザイン開発統括部
エネルギーストレージシステム開発部
エネルギーストレージシステム開発課
チーフエンジニア
松本 充功
大金からバトンを受け取った松本は、2002年に入社以来FCEVの開発に15年ほど従事。2016年からバッテリー開発部門に移り、現在はバッテリーパックシステム開発全般を担当するグループリーダーを務めている。
そもそもなぜ、小型で薄型のバッテリーパッケージを開発するのか。ここにも、Hondaが掲げる理念が大きく関係している。人のためのスペースは最大に、メカニズムのためのスペースは最小にという「M・M思想(Man-Maximum、Mecha-Minimum)」を実現するためだ。
バッテリーパックシステムの開発においては、上記スライドで示したようにさまざまな要素を考慮した上で進めており、本講演ではその中から安全性について解説した。
まずは、短絡(ショート)時の対策である。BEVはHEVに比べ大きな電流が流れる。そのため万一の短絡時に他の部品を破損したり、発煙や発火したりといったトラブルを防ぐため、素早く電流を遮断することが求められる。
そこで松本らは、火薬がスイッチを押し上げる仕組みを使ったメカヒューズ(パイロヒューズ)を採用した高速遮断システムを構築した。
松本が長年にわたり携わっていたFCEVの技術が使われており、「Hondaが培ってきた技術が転用されている、いい事例だと思います」と、述べた。
バッテリーパックは車室の床下に配置されることが多いため、縁石や、悪路を走行した際の玉石からの入力といった、直接的なダメージから守る必要もある。
そこでアンダーカバーとバッテリーパックの間に、インシュレーターという部材を配置。インシュレーターの仕様においてはCAE (Computer Aided Engineering)を活用した。三現主義に則り、実測値とのコリレーションを十分にとりながら検討することで最適値を探った。
最後は、バッテリー内部で短絡が発生した際などに、最悪の場合は発火につながる恐れのある熱暴走に対する取り組みだ。
前提として、熱暴走が発生した際には乗員が危険な状態に陥る5分前に警報を出すことが、法規で定められている。
法規を遵守するために、松本らは模擬試験も含めて50回以上のテストを行った。開発当初はバッテリーパックから火炎が流出してしまい、さらには発火により設備がダメージを受け使えなくなってしまうなど、一筋縄ではいかなかった。
しかし、開発をストップさせることはなかった。近隣の採石場でテストを続けたからだ。このような努力の甲斐もあり、無事、目標を達成する仕様を見つけることに成功した。
「泥臭く徹底的にテストを行ってきましたが、採石場を使うなどフットワークが軽いのもHondaならではだと思います」と松本は述べ、セッションを締めた。
メガキャスト、FSWなどの技術を活用し効率よくバッテリーパックを生産
エネルギーシステムデザイン開発統括部
エネルギーストレージシステム開発部
エネルギーストレージシステム開発課
チーフエンジニア
冨沢 佑一
続いて登壇した冨沢 佑一は、入社以来20年近くにわたり、歯車の生産技術開発業務に従事してきた。2020年から開発部門に移り、現在はバッテリーパックの構造設計のチーフエンジニアとして、次期モデルのバッテリーパック開発を担当している。本講演でもバッテリーパックの生産について紹介した。
現在Hondaでは、従来のエンジン車を開発してきた生産ラインを活用し、BEVの生産も行っている。今後は、シンプルな構造のEVに合わせた、専用の生産ラインを構築していく計画だ。従来のバッテリーケースは多くの部品を組み合わせる構造になっていたためコスト面での課題があった。
複雑な形状の部品を一体成型することが可能なメガキャストなどの技術を採用した。
既にバッテリーケースを効率よく生産するための大型の鋳造機を導入しており、講演ではマシーンが稼働しバッテリーケースを鋳造する動画も紹介されているので、より詳しく知りたい人はアーカイブ動画を見ることをおすすめする。
もう一つの技術がFSW(Friction Stir Welding)と呼ばれるものだ。バッテリーの充電、特に急速充電時などには発熱を伴うため、ウォータージャケットと呼ばれる熱をコントロールするための水路を設ける必要があるが、その際に溶接などを使わずに行える技術である。
ただ、こちらの技術も当初はケースが変形するなど、うまくいかなかったと冨沢は苦労を口にした。解決策は、ここでもワイガヤだ。「メンバーが喧々諤々、本音で意見を出し合うことで何とか解決策を見つけることができました」と、述べた。
冨沢は衝突時におけるバッテリーの安全性についても紹介した。前面や後面での衝突の際はボディやフレームで力を分散する一方、側面からの場合は衝撃吸収材を入れて対応している。
最後に冨沢は、実際に開発に至ったバッテリーパックの現物を紹介。「EVバッテリーシステムの開発は難しく実際には試行錯誤の繰り返しですが、今後も技術進化を続けていきます」と力強く語り、セッションを締めた。
【Q&A】参加者からの質問に登壇者が回答
セッション後は、イベント参加者からの質問に登壇者が回答した。抜粋して紹介する。
Q.EVは構造がシンプルとのことで、開発も楽になっていくのか?
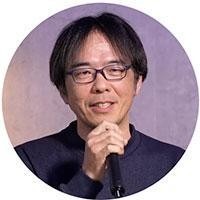
確かに部品点数は少なく構造もシンプルですが、開発が楽になるとは考えてはいません。シンプルだからこその開発の難しさもありますし、品質を担保することも楽ではないからです。ただ、我々にはこれまでの自動車開発で培ってきた技術がありますから、これらをBEVでも活用していきます。
Q.Hondaが自社開発を進める領域の優先度の基準などは?
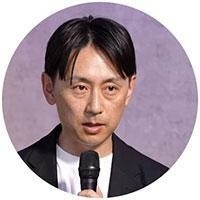
自社開発は工数もコストもかかります。そのため競争力が担保できる領域に注力しようとの考えで進めており、結果として現在はバッテリーの自主開発を進めています。
Q.熱暴走対応の解析は実際に実験を行ったのか、あるいはモデルベース開発(MBD)を用いたのか?
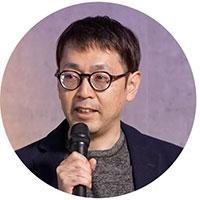
今回は実験で行いましたが、MBDの技術構築にも取り組んでおり、今後は活用していこうと考えています。一方で、熱暴走の事象はバッテリーパック全体に火炎が延焼してしまうと十分な実験データが取得できないため、コリレーションを取るのが難しいです。そのため工夫しながらデータを集め、技術構築している段階です。
Q.衝突した際などバッテリーはどの程度までの変形を許容しているのか?
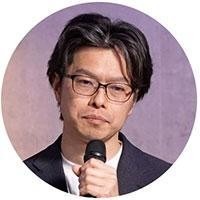
基本的にはバッテリーは変形しない。中のバッテリーはあくまで守る。このような考えで開発を進めています。
Q.ウォータージャケットを薄くすると水量が減ってしまうのではないか?
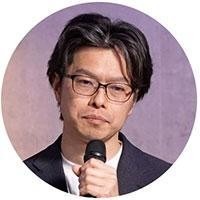
するどい質問です。紹介したFSWの技術は、実現できる設計強度をベースに断面、水路幅などをギリギリのところまでコントロールすることで、薄型ではありますが、多くの水量を確保することにチャレンジしました。設計の腕の見せ所とも言えると思います。
Q.GSユアサと合弁会社を設立した狙いは?
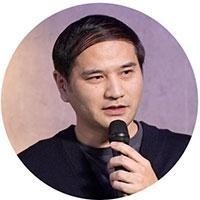
これからの自動車開発は電池がキーになるだろうと考え、電池に関する技術をきちんと開発していく。そのために組織の垣根を超えることで、よりよい商品が実現できるだろうと考え、設立しました。
本田技研工業株式会社
https://www.honda.co.jp/
本田技研工業のキャリア採用情報
https://www.honda-jobs.com/
本田技研工業の採用情報
https://global.honda/jp/jobs/?from=navi_footer_www
本田技研工業の電池・パワーエレクトロニクス領域について
https://www.honda-jobs.com/about/esd/
※記載内容は2025年3月時点のものです